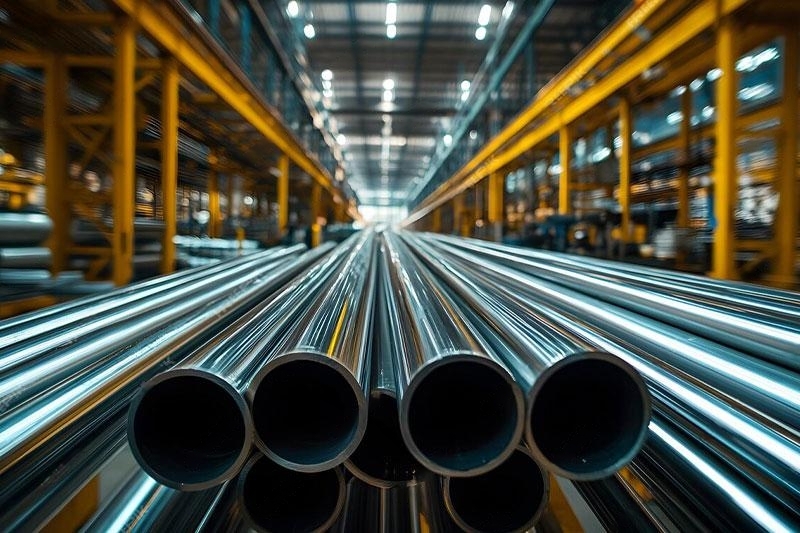
Tubes refer to hollow, cylindrical structures made from
various materials, used in a wide range of applications in construction,
plumbing, industrial processes, and more. Tubes differ from pipes in that they
are often specified by their outer diameter and wall thickness rather than by
their internal diameter. Key aspects of tubes include:
1. Materials:
- Steel Tubes:
- Carbon Steel: Commonly used for structural applications,
transportation of gases and liquids, and in mechanical systems due to its
strength and durability.
- Stainless Steel: Resistant to corrosion and high
temperatures, used in applications like chemical processing, food and
beverage industries, and medical devices.
- Galvanized Steel: Steel tubes coated with a layer of zinc to
prevent rust, used in outdoor applications and plumbing.
- Aluminum Tubes:
- Lightweight and corrosion-resistant, often
used in aerospace, automotive, and construction industries for
applications requiring high strength-to-weight ratios.
- Copper Tubes:
- Highly conductive and corrosion-resistant,
widely used in plumbing, heating, and refrigeration systems.
- Plastic Tubes:
- PVC (Polyvinyl Chloride): Used for water and sewage pipes, electrical
conduits, and various industrial applications due to its chemical
resistance and cost-effectiveness.
- PE (Polyethylene): Flexible and durable, often used for gas
pipelines, irrigation systems, and in medical devices.
- Composite Tubes:
- Made from a combination of materials like
fiberglass, carbon fiber, or reinforced polymers, offering a balance of
strength, flexibility, and lightweight properties.
2. Types and Shapes:
- Round Tubes: The most common shape, used in structural applications, piping
systems, and for mechanical purposes.
- Square and Rectangular Tubes: Used in construction and manufacturing for
frameworks, supports, and other structural applications where a flat
surface is beneficial.
- Oval and Other Shapes: Used in specialized applications such as
automotive and aerospace, where aerodynamics or aesthetics are important.
3. Applications:
- Construction:
- Structural Support: Tubes are used as columns, beams, and
trusses in buildings and bridges due to their ability to handle
compression and tension.
- Scaffolding: Steel tubes are commonly used to create temporary scaffolding
structures for construction projects.
- Plumbing and Piping:
- Water Supply: Copper, PVC, and PEX tubes are used to
carry water in residential, commercial, and industrial plumbing systems.
- Gas and Oil: Steel and polyethylene tubes are used to transport natural
gas, oil, and other fuels over long distances.
- Mechanical Systems:
- Hydraulic and Pneumatic Tubes: Used in systems that rely on fluid power to
operate machinery, such as in automotive and industrial equipment.
- Exhaust Systems: Steel tubes are used in automotive exhaust
systems to carry gases from the engine to the outside of the vehicle.
- Industrial Applications:
- Heat Exchangers: Tubes made from materials like copper or
stainless steel are used in heat exchangers to transfer heat between
fluids.
- Manufacturing: Tubes are used in the manufacturing of
products ranging from furniture to machinery parts.
- Aerospace and Automotive:
- Frames and Chassis: Lightweight aluminum and composite tubes
are used in the construction of vehicle frames and chassis for cars,
motorcycles, and aircraft.
- Roll Cages: Steel tubes are used in roll cages for racing cars to protect
drivers in the event of a rollover.
4. Manufacturing
Processes:
- Seamless Tubes: Manufactured by extruding or drawing solid
metal billets into a tube shape without a welded seam, offering high
strength and durability, particularly in high-pressure applications.
- Welded Tubes: Created by rolling a flat strip of metal and welding the edges
together. They are more cost-effective than seamless tubes and are used in
applications where the seam does not compromise the integrity.
5. Surface Treatment
and Coating:
- Galvanization: Coating steel tubes with zinc to protect
against corrosion, especially in outdoor or industrial environments.
- Powder Coating: Applying a dry powder to tubes followed by
heating to create a durable finish, often used for aesthetic purposes and
additional protection.
- Anodizing: An electrochemical process that increases the thickness of the
natural oxide layer on aluminum tubes, enhancing corrosion resistance and
appearance.
6. Quality Control and
Standards:
- Testing: Tubes undergo various tests such as pressure testing, tensile
testing, and corrosion resistance testing to ensure they meet required
standards.
- Standards: Tubes are manufactured according to international standards
such as ASTM, ISO, and DIN, which define specifications for dimensions,
materials, and performance.
Tubes are a versatile
component in many industries, valued for their ability to convey fluids,
provide structural support, and contribute to the manufacturing of a wide range
of products. Their selection and use depend on factors like material, size, shape,
and the specific requirements of the application.